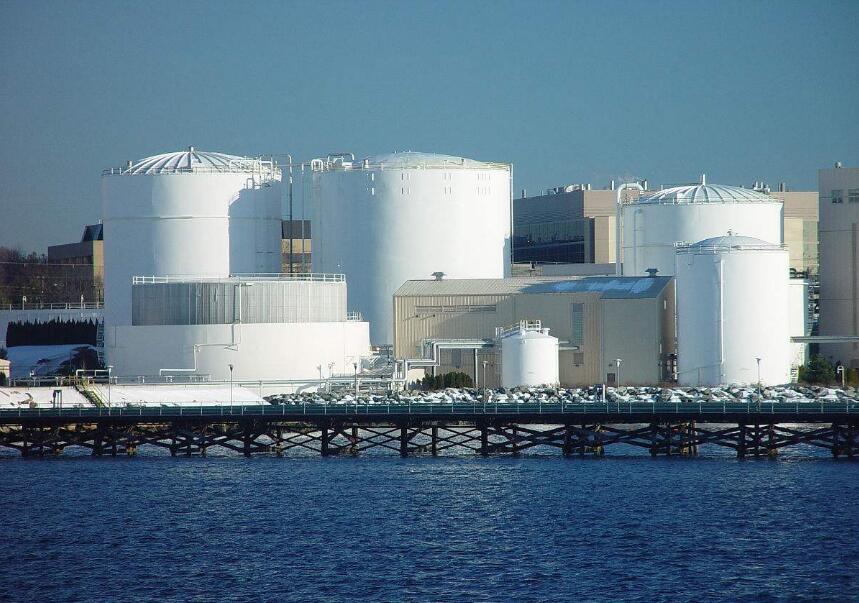
在石化生产中,原油、成品油、轻烃等的存储、计量、核算和管理是非常重要的环节。围绕着储罐乃至整个罐区的监控与管理,是储运作业中最基本的工作内容。提高储运自动化及其管理水平,对企业减少损耗、降低成本、增加效益具有明显的作用。
1监控要求
1)信号采集:标准信号的采集;对钢带液位计非标准信号数据的采集,并通过软件加以处理和运算,达到原仪表的技术要求;对具备智能通讯接口的光导液位计、雷达液位计、伺服液位计等数据的采集和转换处理。2)监控操作:操作控制;参数设定;阀门自动开启与关闭;油品在线调合,变频技术应用。3)动态显示:运转设备的状态显示,能够远程监控机泵等设备的运行情况;报警显示;趋势显示。4)操作画面:罐容量表的查询与管理;打印实时报表和历史报表,并可任意设定打印时历史报表的时刻。5)系统具备可扩展性。
2系统方案
2.1控制站
DCS集散控制系统采用Honeywell的TPS技术,由局部控制网络(LCN)和综合控制网络(UCN)两种通讯网络组成。LCN网上有操作站(GUS),历史模件(HM)。UCN网上有高性能过程管理器,LCN网与UCN网之间通过网络接口模件“NIM”连接。光导液位计和钢带液位计具有智能通讯接口,阀门的状态检测和控制使用标准的干接点信号。
1)开关量控制。对于现场电磁阀控制、电磁阀回讯及报警信号检测采用c200h系列的DCS完成,力控i/o驱动程序负责完成DCS数据的读/写。2)标准4~20ma信号。各种压力、流量的标准4~20ma信号通过DCS模拟量卡件的转换,再经过DCS的通讯接口传送到操作站的监控软件中。3)智能通讯传送。钢带液位计由于从一次仪表输出的信号是一组串行bcd码,计算机操作站不能直接接收该bcd码,必须使用智能转换器sbb-100,将现场一次表传送的串行bcd转换成数字信号,通过rs-485将数据传送到操作站上。光导液位计和温度巡检仪采用rs-485直接与操作站上的软件通讯。
2.2操作站
操作站操作系统采用windows2000,包括液晶显示器(LED)、PC键盘、光电鼠标、主机箱。PC键盘上的F1―F12可以自定义为流程图等快捷键,仪表应具备标准输出信号或智能通讯功能,操作站内增加RS485通讯接口卡连接智能仪表。
3软件设计说明
根据工艺提出的生产要求,HONEYWELL软件操作画面的设计采用主菜单的形式,在每幅画面下分别有按纽进行切换,画面包括主菜单画面、动态流程画面、操作画面、报表画面、罐容量表、报警等。
3.1设备动态显示
机泵压力、电流信号,将现场信号通过4~20ma电流,赋予标准量程传入DCS系统中,根据不同数值赋予流程图中机泵不同颜色定义,便于操作监控。
各阀门控制包括控制信号和回讯信号,当操作完成后,现场回讯设备触及回讯开关,将现场的回讯状态反馈回来,在系统中红色代表阀门关闭,绿色代表阀门打开,以此便于区分。
3.2报警的处理
在系统报警设置分为硬件报警和软件报警两部分,硬件报警是在现场设置独立的报警仪表,一旦发生危险情况,自动触及现场报警开关,现场通过仪表线将开关信号传到系统中,实现画面报警。软件报警有两种方法:一是在DCS的组态中设置高、低限报警值,一旦数据超出范围,发生画面、声音报警;二是在流程图画面中设置报警值,根据现场远传信号的数值,并赋予不同的颜色定义,来表示报警程度的高低。
3.3油品在线调合控制
采用油品在线优化调合和智能加剂技术,首先将各汽油调合的组分油收入到各组分罐,利用泵将各组分油经混合器送入到调合管线中,通过近红外在线质量分析仪监控质量油品的性质,控制软件根据分析仪反馈回来的质量情况重新分配各调合组份比例,直到达到质量过剩最小、成本最低的要求为止;加剂系统与汽油调合系统同时使用,加剂贯穿调合全过程,实现精确、均匀控制。该系统可以实现增加汽油一次性调合成功率,降低了优质汽油组分的添加和能耗。
3.4罐区MES系统
MES生产运行系统的英文全称是Manufacturing Execution System,简称MES,是美国管理界上世纪九十年代提出的新概念。MES能通过信息传递对从订单下达到产品完成的整个生产过程进行优化管理。MES同时还能通过双向的直接通讯在企业内部和整个产品供应链中提供有关产品行为的关键任务信息。随着计算机技术和网络技术的迅速发展,流程工业控制中出现了多学科间的相互渗透与交叉;MES在储运系统罐区应用中,提供了完善罐量计算功能,系统内设置了罐量容积表及罐量计算公式,通过输入当前的液位、温度、密度值,系统自动计算罐存量,并可根据输入描述的产品种类,自动归类,生成报表,计算同品产品的总库存,此外系统包括水电气风等能耗数据及环保数据的录入和考核功能,并且使数据资源网络共享,便于查询、管理,统一控制和协调调度。
3.5变频调速技术
机泵的流量等参数需经常进行调节,传统的调节方法是:调节进出口管路的阀门或挡板开度,调节流量大小,应用旁路调节或采用调速电机通过调节电压改变电机转速。这些调节方法,虽能满足化工工艺要求,但节流损失大,设备效率降低,属于高耗能调节方法,虽然流量降低了,但消耗功率不降低。采用变频调速技术控制,通过设置PID调节参数,根据偏差动作大小,调整变化反应速率,消除余差,改变电机的转速,改变机泵的性能曲线,不仅流量等参数调节灵敏可靠,节电效果良好,而且给生产操作带来了方便,使设备运行更加平稳,延长了使用寿命,为正常生产提供了可靠的保证。此外,变频调速还具有软启动功能,启动转速可以从零开始逐渐升高,因此带负荷直接启动不会有较大的起动电流,避免了启动前先关闭出口阀的要求,方便了操作,且对电网冲击小,可实现平稳启动。
4系统调试及运行情况
应用脚本程序编制时,一定要考虑通讯的速度,不停地循环向控制器(DCS)下置数据会影响采集速度,因此,向DCS发送控制命令的程序动作应尽量放在数据改变脚本中执行。
系统参数的配置根据不同的设备可反复调整使之达到最佳工作状态,因为不同的设备对采集速率有不同的要求。
重要的控制功能放到稳定可靠的DCS去完成,操作站出现故障时不会影响控制,做到危险实际应用结果表明,系统运行稳定,操作简洁方便,有效地降低了工人的劳动强度,减少了盘装仪表的维护量,达到了预期的控制效果。为装置的安全、稳定和长周期运行发挥了极大的作用。
5结束语
罐区自动化监控系统、自动化罐区连锁的设计与应用极大地提高了罐区的监控与管理效率,对于保证企业安全生产,降低生产成本,减轻人工劳动强度,提高经济效益起到了很大的作用。